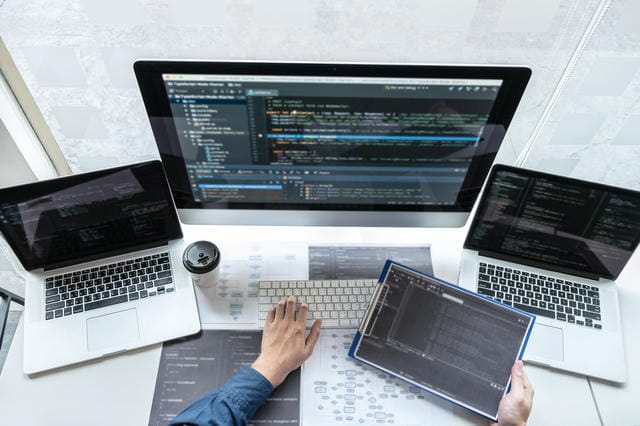
小型化や高機能化が求められる現代の電子機器には、不可欠な要素として特殊な部品が組み込まれている。その中でも中心的役割を果たすのが、複数の電子部品を効率よく接続するための基盤である。これらは絶縁素材の板上に金属パターンを形成し、各部品どうしを電気的・機械的に接続・固定できるため、電子回路の設計や製造に革命をもたらした。この基盤の製造に取り組むメーカーは、長年にわたり多様な技術を蓄積し、安定した品質確保と効率的な量産の両立を目指している。製造工程には複数の重要な段階が存在し、その一つ一つが全体の性能や信頼性に直結している。
具体的には、ガラス繊維などで強化された絶縁板材へ一定の厚みを持つ銅箔をラミネートし、その後回路パターンに沿った化学薬品処理や露光・現像プロセスを施すことで、精密な銅配線が形成される。そして表面実装に適した状態にするために、クリーム状はんだや絶縁被膜の塗布、リフロー処理など多彩な加工手法が用いられる。こうした製品を取り巻く環境は年々高度化しており、それに伴い製造するメーカーが担う責務も重くなっている。なぜなら、スマートフォンや自動車制御装置、医療機器やロボットなど、様々な分野において電子機器の多機能化が急速に進行しているからである。その結果、回路設計の密度向上や高周波信号へのノイズ管理、放熱対策など、解決すべき技術的課題が増大している。
また、これらの製品の根幹に関わるのが半導体である。半導体素子は、ディジタル制御や情報通信分野だけでなく、高効率の電力変換や各種センシング技術の中枢を担っている。たとえば、高速動作を実現するためには配線の長さや太さ、間隔にまで拘った設計が必須であり、それを具現化する技術力こそが各メーカーの競争力の源泉となっている。生産工程では、精密な寸法管理が不可欠である。配線幅や穴径など待ったなしの精度が要求され、検査装置による品質管理や環境試験を通過した製品のみが市場に送り出される。
さらに、故障を未然に防ぐための工程管理体制やトレーサビリティの迅速化も重視されている。このような厳しい基準があるからこそ、高い信頼性と安全性が実現できる。近年は環境負荷への対応も急務となり、鉛フリー部品や回収リサイクルシステムの採用が標準化しつつある。材料選定の段階から、長寿命かつ化学的に安定したものを採用するとともに、生産時の廃液処理やリサイクル性にも配慮した開発が推進されている。また、放熱や電磁波対策のための新素材や構造設計も進化しており、従来では難しかった薄型軽量かつ高耐久性の基板も増えている。
動作信頼性確保のため、実装後の検査や評価にも様々な工夫が凝らされている。例えば、画像認識装置や特殊な電気計測器による自動検査、さらには動作温度範囲や湿度変動テストなどによる耐環境性試験が徹底されている。海外需要の拡大にも直結するため、これらの総合的な品質保証体制は継続的に改善・強化されている。また、実装の自動化が加速し、従来人手によって行われていた微細なはんだ付けなども専用ロボットや自動搭載装置に置き換わっている。これにより、一層の高速化や微細化・高密度実装が可能となり、最先端の半導体部品も安定して量産できる素地が整いつつある。
小型化要求や多層化といった市場のニーズに即応するためには、これら製造装置や評価機器への投資も欠かせない。世界的な電子製品の普及に伴い、低コストで高品質なプリント基板の需要は増加している。その一方で、不具合率の低減や短納期対応も喫緊の課題であり、複数の技術者や設計者が一体となって設計・工程開発・品質検証を推進している。こうした分業と協調の仕組みが整うことで、より多様なアプリケーションへ対応可能な体制が確立されてきた。通信や車載分野、医療技術、自動化システムなど、最先端分野での活躍を支えるため、回路設計や信号処理だけでなく熱設計や耐環境性、コスト管理といった多角的な知見が求められている。
そのため、設計段階から量産・評価・納品まで一気通貫で品質管理に努める体制の重要性がますます高まっている。今後も機能の多様化、小型化、高性能化が求められる中、これら基礎技術の最適化や新材料の導入、グローバルな市場対応まで幅広く見据えた技術革新が続けられていく。こうして積み上げられてきた技術やノウハウが、電子機器産業全体の発展を支えている。現代の電子機器にとって、プリント基板は不可欠な中核部品であり、複数の電子部品を効率よく接続し高密度な回路設計を可能にしている。製造には絶縁板への銅箔ラミネートや化学的パターン形成、表面実装のための多様な加工が含まれ、品質や量産性の両立へ各メーカーが技術を磨いてきた。
スマートフォンや自動車、医療機器など用途が広がる一方で、基板には高周波ノイズや放熱など新たな課題への対応も求められ、設計や生産技術の高度化が進む。信頼性確保のため寸法精度やトレーサビリティ管理が徹底され、画像認識や環境試験など多様な検査体制も強化されている。環境規制に対応し鉛フリー化やリサイクルも進み、素材や構造の進化による薄型・高耐久化も顕著である。また、実装工程の自動化や微細化対応で量産効率が向上し、安定した製品供給体制が整備されてきた。こうした分業と協調による総合技術力が、多様化する市場ニーズや最先端分野の要求に応え、電子機器産業全体の発展を支えている。
今後も新材料の導入やグローバル展開を見据えた革新が続く中、基盤技術のさらなる最適化が重要性を増していく。